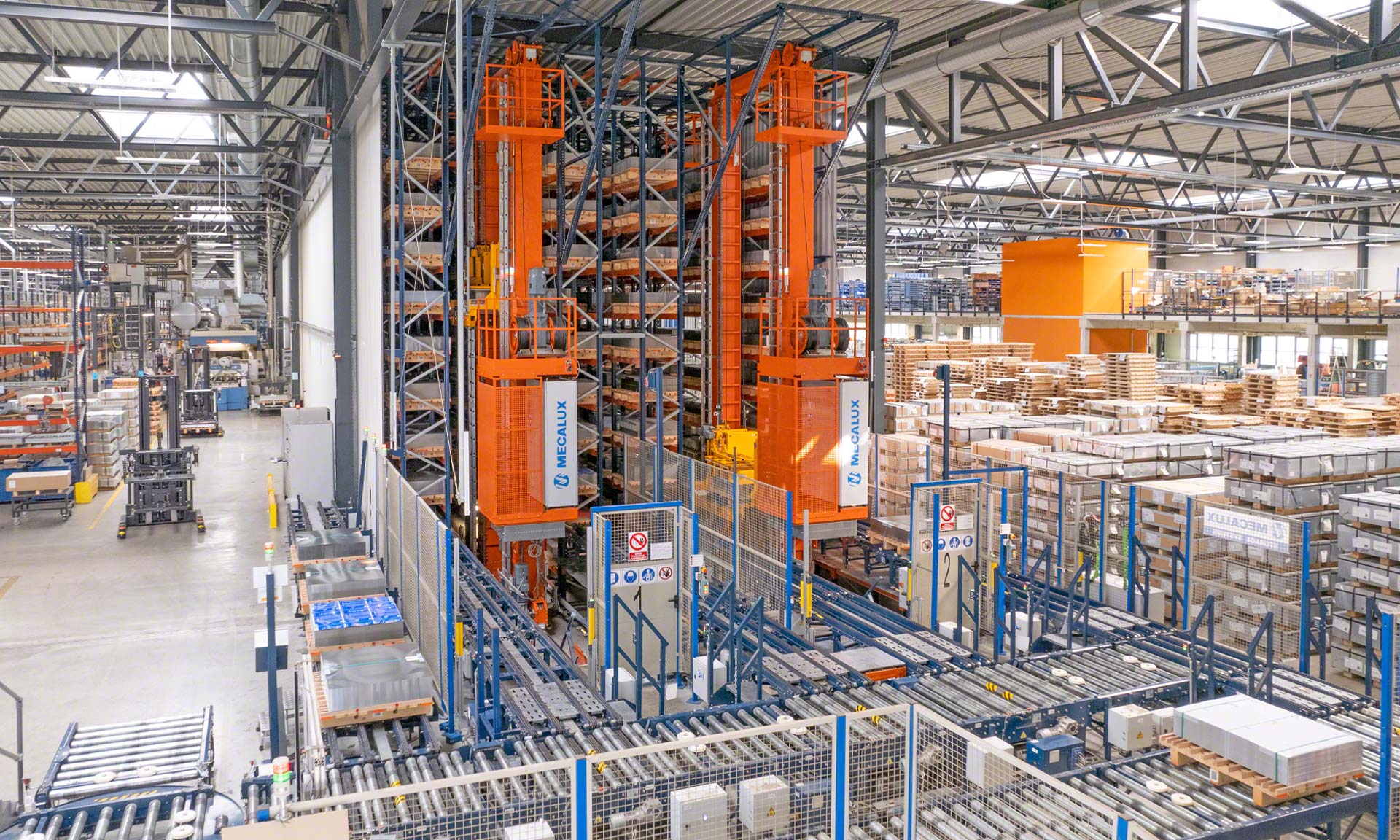
Blechwarenfabrik: la fábrica de envases metálicos más moderna de Europa
Blechwarenfabrik, fabricante de latas de aluminio en Limburg (Alemania), integra todos sus procesos productivos y logísticos en un nuevo centro de 63.000 m² completamente automatizado y digitalizado.
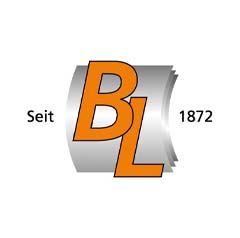
Blechwarenfabrik, fabricante de latas y envases metálicos, ha estrenado nueva sede en Offheim (Alemania) donde produce más de 100 millones de envases al año. El centro se compone de dos depósitos automáticos conectados con producción mediante Easy WMS de Mecalux que organiza el envío de materias primas.
Blechwarenfabrik: tradición e innovación
Blechwarenfabrik es uno de los primeros fabricantes europeos de latas y envases metálicos utilizados en múltiples sectores industriales (mayoritariamente para almacenar y manipular productos químicos).
- Año de fundación: 1872
- Equipo profesional: 500 personas
- Capacidad de producción: más de 100 millones de envases metálicos al año
- Plantas de producción: Alemania, Dinamarca, Rusia y Polonia
RETOS
|
SOLUCIONES
|
BENEFICIOS
|
---|
Blechwarenfabrik, empresa líder en Europa en la producción de envases metálicos para productos químicos, ha automatizado y digitalizado su logística con el fin de afrontar el incremento de las ventas.
En Offheim (Alemania), la compañía posee una nave de 22.000 m² donde todos los movimientos de mercadería están completamente automatizados: vehículos de guiado automático ─más conocidos por sus siglas en inglés, AGV─ conectan los dos depósitos automáticos con las líneas de producción con total autonomía.
Antes, la compañía disponía de dos plantas de producción en Alemania donde fabricaba todos los envases metálicos (latas de hojalata para bebidas, conservas…) y tenía externalizada la logística por la falta de espacio de almacenamiento. “La materia prima se depositaba en el depósito principal y el producto final, una vez salía de las líneas de producción, se llevaba a un depósito ubicado a 5 km de distancia”, explica Christoph Weber, responsable técnico en Blechwarenfabrik.
Decidida a limitar la dispersión logística, a reducir costos y a centralizar todas las actividades en un mismo espacio altamente digitalizado y sostenible, Blechwarenfabrik se embarcó en su proyecto más ambicioso hasta la fecha: la construcción de una nueva sede en Offheim (Limburg), donde desarrollar toda su actividad. En las modernas instalaciones se encuentran las oficinas, 25 líneas de producción y una zona de almacenamiento. En la fábrica se procesan 22.000 toneladas de acero que sirven para fabricar más de 100 millones de envases metálicos al año.
El proceso de centralización, tanto de la logística como de la producción, se ha llevado a cabo de manera escalonada porque algunas de las fases productivas han tenido que reconfigurarse y adaptarse al nuevo emplazamiento. Los responsables de Blechwarenfabrik trabajaron codo con codo con el equipo técnico de Mecalux a fin de encontrar una solución personalizada. “Un proyecto de gran envergadura como el nuestro no es fácil de llevar a cabo, porque teníamos que considerar muchos detalles. Con la ayuda de Mecalux, el traspaso de todas las operativas logísticas a nuestra nueva planta se ha hecho a la perfección”, sostiene Weber.
Robótica para una mayor eficiencia y sostenibilidad
Si algo tenía claro la compañía es que quería apostar por la industria 4.0, dotándose de la tecnología para integrar producción y logística de modo automático. "Antes, la gestión de las operativas y los movimientos de mercadería eran manuales. Los operarios abastecían producción con la ayuda de carretillas. Además, nuestras instalaciones se dividían en distintas plantas, lo que dificultaba la logística interna”, señala el responsable técnico.
Ahora, producción y almacenamiento se concentran en una misma planta y hasta quince vehículos de guiado automático trasladan los productos de un punto a otro de la nave con la mínima intervención de los operarios. Los robots reciben las instrucciones del sistema de gestión de depósitos (WMS) para saber dónde llevar los productos. “Hemos automatizado la gestión de la mercadería, desde la entrada hasta el despacho de los productos. En colaboración con Mecalux, hemos construido la fábrica de envases metálicos más moderna de Europa”, comenta Weber.
Minimizar el impacto medioambiental de los procesos productivos y logísticos ha sido desde siempre una de las principales preocupaciones de Blechwarenfabrik. Al centralizar todos los procesos en un mismo espacio y, por tanto, evitar el traslado de mercadería entre plantas de producción y depósitos, la compañía prevé dejar de emitir 2.600 toneladas de gases contaminantes al año.
La planta de Blechwarenfabrik también cuenta con un área donde se agrupan los residuos metálicos que se han generado durante los distintos procesos industriales con el fin de reciclarlos. Asimismo, en el tejado de la fábrica se han instalado 4.100 paneles solares que generan energía utilizada en el proceso de producción y almacenamiento.
Logística y producción: conexión eficiente con Easy WMS
La nueva planta de Blechwarenfabrik se compone de dos depósitos automáticos: uno en el interior de la nave destinado a las materias primas y otro autoportante para los productos terminados. Los depósitos autoportantes son edificios formados por los racks que soportan su propio peso, el de los cerramientos verticales y la cubierta, además del de la mercadería. También ha implementado el sistema de gestión de depósitos Easy WMS de Mecalux, un sistema que gestiona y optimiza todos los procesos en ambos depósitos.
“Integrar producción y logística ha sido uno de los mayores retos de este proyecto. Lo hemos logrado al haber transferido de forma progresiva los procesos productivos a las nuevas instalaciones. Así hemos podido analizar y resolver las incidencias a medida que iban surgiendo”, explica Uwe Wonsack, director de Operaciones de Blechwarenfabrik.
Para fusionar logística y producción con eficiencia, la compañía emplea el sistema Easy WMS. El programa de Mecalux se conecta con el ERP Infor de Blechwarenfabrik y el sistema de control de producción (MES) para conocer qué artículos se necesitan en producción y organizar su distribución. “Los programas se apoyan entre ellos. Si buscamos información sobre los productos, Easy WMS nos facilita todos los detalles, la cantidad disponible o la ubicación exacta”, afirma Wonsack. El ERP, a su vez, se conecta con otros sistemas que intervienen en los procesos productivos como, por ejemplo, el que gestiona los robots paletizadores utilizados en producción, el que recopila datos sobre el desarrollo de las operativas en fábrica o el que organiza, controla y monitoriza esas mismas operativas.
Easy WMS también se comunica con el programa de control de los vehículos AGV para organizar los movimientos de mercadería entre los depósitos y producción. “Los AGV abastecen las líneas de producción de manera automática. Cuando Easy WMS recibe un pedido desde producción, el sistema organiza su preparación en el depósito. Los AGV recogen los productos y los trasladan hasta la línea que los haya solicitado. El proceso es transparente, rápido y efectivo”, apunta Wonsack.
Además, el sistema de Mecalux organiza la gestión de residuos en la instalación de Blechwarenfabrik. A medida que se generan residuos en los procesos productivos, Easy WMS ordena su envío a la zona de reciclaje.
Sistema de gestión de depósitos: trazabilidad rigurosa
Easy WMS de Mecalux es una herramienta que confiere una total trazabilidad de los productos almacenados. El programa hace un seguimiento exhaustivo de la mercadería, desde que llegan las materias primas hasta que se expiden los productos terminados. Conectar logística y producción mediante Easy WMS ha aportado múltiples ventajas a Blechwarenfabrik:
- Visibilidad y gestión del stock en tiempo real. Easy WMS conoce el estado y la localización exacta de las referencias, tanto materias primas como productos terminados.
- Soporte a la producción just-in-time. El sistema se asegura de enviar las materias primas a los procesos productivos en la cantidad justa y en el momento oportuno.
- Gestión del maestro de artículos y de la lista de materiales. En cada orden de producción se configuran las materias primas necesarias con las que se van a elaborar los productos.
- Mejora de los procesos productivos. Una buena organización de las operativas y un control preciso de la mercadería repercute en una mayor eficiencia y agilidad.
- Trabajo sin papel. Los operarios solicitan las materias primas que necesitan para trabajar desde terminales de radiofrecuencia o mediante tablets.
“El mayor cambio que hemos experimentado con Easy WMS ha sido el control del stock: ahora podemos saber en todo momento dónde se encuentra cada producto”, añade Wonsack. El control del stock ha permitido a Blechwarenfabrik organizar mejor la mercadería, lo que incide también en una mayor fluidez de las operativas. El orden es primordial para que esta compañía asegure el abastecimiento just-in-time de las líneas de producción.
Cadena de suministro totalmente automática
Blechwarenfabrik tenía claro que la automatización le ayudaría a reducir costos y aumentar las prestaciones de la cadena de suministro. La empresa ha optimizado y agilizado los procesos de almacenamiento, preparación y despacho de la mercadería.
Transelevadores, transportadores de pallets y vehículos automáticos AGV proporcionan un movimiento permanente y controlado de mercadería. Cada día se envían 600 pallets con materias primas a las líneas de producción y, al mismo tiempo, 1.200 pallets con aproximadamente 500.000 latas y envases metálicos se recogen de las líneas de producción, se almacenan y se ponen a disposición para su envío a cientos de clientes que la compañía tiene repartidos por Europa.
➤ Depósito de materia prima
De 11 m de altura y 100 m de longitud, el depósito automático está compuesto por dos pasillos con racks de simple profundidad a ambos lados capaces de alojar 2.500 pallets con las láminas metálicas empleadas en la fabricación de las latas.
El depósito recibe una media de 125.000 láminas metálicas al día que han enviado los proveedores de Blechwarenfabrik. En conexión permanente con el sistema MES (Manufacturing Execution System), lo primero que hace Easy WMS al organizar las entradas es ordenar que las láminas se coloquen sobre el pallet adecuado y en la posición correcta. En función del artículo que se va a fabricar en las líneas de producción, cada lámina se debe situar en una posición u otra sobre el pallet.
“La mercadería se organiza siguiendo el criterio FIFO, es decir, el primer pallet en entrar es el primero en salir. De esta manera, evitamos que los artículos se queden obsoletos y podemos asegurar un flujo continuo de mercadería”, señala Wonsack.
Para estar seguros de que las líneas de producción dispongan de la mercadería necesaria, Easy WMS comprueba el número de láminas que necesita cada orden y cuál es la posición requerida. En el caso de no contar con una cantidad suficiente, se seleccionan otras láminas del depósito y se llevan a la máquina volteadora, donde se indica a los operarios cómo colocar las láminas en la posición correcta.
Siguiendo las indicaciones de Easy WMS, los vehículos AGV recogen las láminas en alguno de los dos puestos de salida del depósito automático y las trasladan automáticamente hasta unos racks selectivos cercanos a las líneas de producción.
Estos racks actúan como búfer, pues almacenan las materias primas de forma temporal hasta que se usen en las líneas de producción. Una vez que la ubicación se ha vaciado, se puede volver a ocupar con otro artículo para la siguiente orden de producción.
➤ Líneas de producción
Cuando comienzan los procesos productivos, Easy WMS ordena a los robots AGV el envío de las materias primas y los productos semielaborados a las líneas correspondientes.
Uno de los productos semielaborados que se requieren en las órdenes de producción son los cuerpos de las latas (denominados “bodies”). Estos artículos no se alojan en el depósito automático, sino que se depositan directamente en los racks selectivos junto a las líneas de producción. Easy WMS también hace un seguimiento de estos productos y ordena su envío a producción en el momento oportuno.
En producción, los operarios pueden comunicarse con Easy WMS para, por ejemplo, pedir pallets vacíos, notificar si hay stock defectuoso o devolver materias primas que hayan sobrado al depósito.
“Es muy importante para nosotros que los operarios de las líneas de producción no tengan que hacer tareas secundarias y puedan centrarse en su trabajo principal. A través de un terminal, los operarios pueden solicitar los productos a Easy WMS”, añade Wonsack.
Siguiendo las órdenes de Easy WMS, los AGV también recogen los residuos y los llevan automáticamente hasta la zona de reciclado.
➤ Depósito de producto terminado
Con capacidad para 18.000 pallets, el depósito automático autoportante mide 31 m de altura y está compuesto por cuatro pasillos con racks de doble profundidad en ambos lados.
Cada hora llegan alrededor de 80 pallets procedentes de las líneas de producción. Antes de entrar en el depósito, estos productos superan un puesto de inspección en el que se verifica que cumplan los requisitos establecidos para su ubicación en los racks.
A continuación, Easy WMS asigna una ubicación a cada producto. El sistema incorpora reglas y algoritmos para decidir cuál es la mejor ubicación para cada pallet teniendo en cuenta su referencia y rotación.
En cuanto a los despachos, el ERP notifica a Easy WMS qué pallets han de distribuirse y, a continuación, el SGA asigna un muelle a cada orden de salida. Cada hora, 100 pallets salen de este depósito para dirigirse a la zona de preparación de pedidos o directamente a los muelles. “Los procesos de despacho funcionan a la perfección”, afirma Wonsack.
En la parte frontal del depósito, se ha habilitado un puesto de picking. Allí, se preparan los pedidos siguiendo el principio “goods to person”, es decir, los operarios permanecen a la espera de recibir las referencias que precisan para preparar cada pedido. Los operarios extraen las cajas de los pallets procedentes del depósito y las depositan en otro pallet donde se agrupan los artículos que conforman el pedido.
Los operarios disponen de una pantalla y de terminales de radiofrecuencia para seguir paso a paso las indicaciones de Easy WMS. Con estos dispositivos, están informados en todo momento sobre qué productos extraer de los pallets y en qué pedidos colocarlos. Como resultado, Blechwarenfabrik ha minimizado la posibilidad de cometer errores.
Por su parte, los pallets que se envían directamente al despacho, se etiquetan y son conducidos hasta el muelle correspondiente. También se ha habilitado una zona de precargas en el suelo donde los pallets se agrupan y clasifican en función del pedido al cual corresponden o a la ruta de transporte, a fin de agilizar su carga en el camión de distribución.
Industria 4.0 en pro de la eficiencia y la sostenibilidad
Blechwarenfabrik ha asegurado y potenciado su ritmo de crecimiento a través de la tecnología. La compañía se ha adentrado en la industria 4.0 con el objetivo de llevar un control más exhaustivo de los procesos y prestar un servicio más eficiente a sus clientes. Con la ayuda de la automatización, la firma no solo ha incrementado su rendimiento, pudiendo producir más de 100 millones de envases al año, sino que también se ha beneficiado de una cadena de suministro más sostenible.
Con las soluciones automáticas de Mecalux y la gestión de Easy WMS, la empresa dispone de una cadena de suministro interconectada. Todos los procesos están coordinados por el sistema con un propósito: atender las líneas de producción en el momento preciso. Digitalización y automatización son una combinación que significa éxito para Blechwarenfabrik y que, sin duda, contribuirá a que la firma siga creciendo en un futuro.
Cuando inauguramos nuestra nueva planta en Offheim (Limburg), teníamos claro que debíamos impulsar la automatización. Con la tecnología de nuestro socio Mecalux, nuestra cadena de suministro ha logrado un gran avance.
Galería
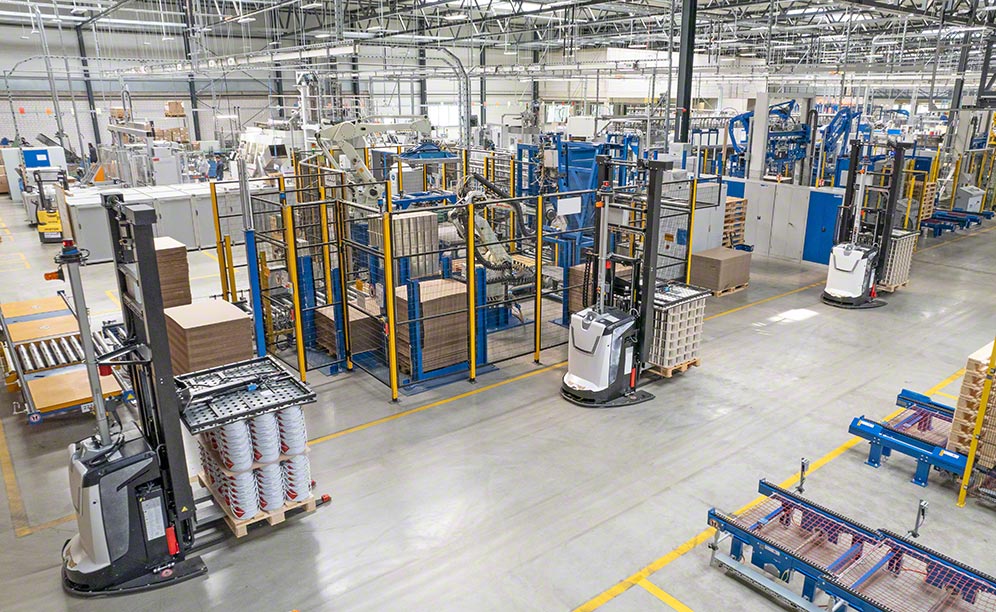
Consulte con un experto