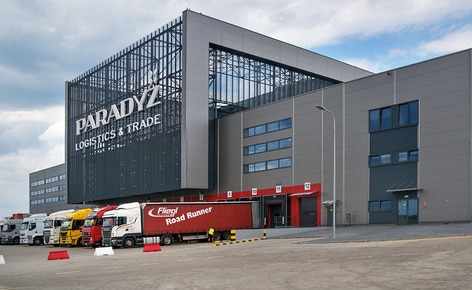
Ceramika Paradyż refuerza su apuesta por las últimas tecnologías con su nuevo depósito automático autoportante en Polonia
Alta capacidad y agilidad en el picking en el depósito automático autoportante de Ceramika Paradyż
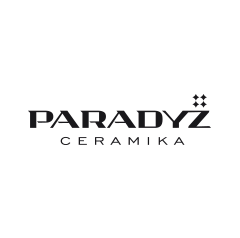
Mecalux ha proyectado para Ceramika Paradyż un depósito automático autoportante con capacidad para más de 20.200 pallets en la localidad de Tomaszów Mazowiecki (Polonia). En la cabecera del depósito hay un edificio de dos plantas que permite organizar con eficiencia la entrada y salida de la mercadería, a la vez que agilizar la preparación de pedidos. En el suministro, se engloba el software de gestión de depósitos Easy WMS de Mecalux.
Necesidades de Ceramika Paradyż
Ceramika Paradyż es un importante fabricante de cerámicas polaco que exporta sus productos a más de 50 países de todo el mundo.
La compañía es reconocida por introducir la última tecnología en todos sus procesos productivos con el fin de ofrecer productos innovadores y de la máxima calidad.
Con vistas a reforzar su ritmo de crecimiento en el futuro, contrató a Mecalux la construcción de un depósito automático de gran capacidad, en el que se ha incluido un área de picking donde preparar los pedidos con agilidad.
Solución de Mecalux
Tras estudiar en profundidad los requerimientos de Ceramika Paradyż, el equipo técnico de Mecalux ha diseñado y construido un depósito automático autoportante que se ajusta a los requisitos planteados por la empresa.
El depósito mide 25 m de alto, 97 m de longitud y 35 m de ancho y está constituido por ocho pasillos con estanterías de simple profundidad a cada lado.
Con esta solución, la compañía ha conseguido la capacidad de almacenaje precisa para abastecer a su mercado, localizado principalmente en Europa.
Adosado al depósito, se ha construido un edificio de menor altura que está distribuido en dos plantas donde se efectúan operativas distintas.
En el nivel inferior se encuentran las entradas y salidas de la mercadería. Se han instalado puestos de inspección, un remontador y dosificador de pallets vacíos, así como los canales de precarga.
En el superior se preparan los pedidos. Se ha habilitado toda un área dotada de un circuito de electrovías, lanzaderas, puestos de picking, búfer de pallets y una zona de consolidación y enfardado.
El depósito
El depósito de 3.290 m2 está compuesto por ocho pasillos con estanterías de simple profundidad a ambos lados. En longitud, disponen de un total de 45 módulos con catorce niveles en altura que admiten dos pallets cada uno.
Las referencias se depositan en las ubicaciones correspondientes en base a los criterios de rotación A, B y C, lo que permite optimizar los movimientos de los equipos de manutención.
Al ser de construcción autoportante, las estanterías deben soportar su propio peso y de la mercadería, a la vez que el de los cerramientos verticales y la cubierta. A la hora de ser diseñada, también se han previsto otros factores que interactúan sobre la estructura, como la fuerza que transmite el viento, el grado sísmico de la zona en cuestión y la normativa local vigente.
Entrada y salida del depósito
El depósito posee dos niveles para la entrada y salida de la mercadería.
El inferior coincide con la planta baja del edificio anexo y es donde se produce la entrada de la mercadería procedente del centro de producción, así como la salida de pallets completos y pedidos finalizados con dirección al área de expedición.
En la planta superior, que también coincide con el nivel superior del edificio anexo, se realiza la salida de los pallets necesarios para el picking y la entrada de los pedidos que han sido terminados.
En cada pasillo, los transelevadores mueven la mercadería desde los peines de entrada y salida de ambos niveles hasta las ubicaciones en las estanterías que ha asignado el software de gestión de depósitos Easy WMS.
Estos equipos son del modelo monocolumna MT3 y trabajan a una velocidad de traslación de 220 m/min y 54-66 m/min en elevación.
El edificio anexo
Planta superior Área de picking
La planta superior del edificio anexo al depósito está destinada íntegramente a la preparación de pedidos. Esta amplia zona está conformada por seis puestos de picking y en un futuro se podrán integrar cuatro más, en función de la demanda y las necesidades logísticas de Ceramika Paradyż.
Para facilitar las maniobras de los operarios, estos disponen de equipos auxiliares, como las mesas que se elevan hasta una posición ergonómica y los manipuladores de cajas mediante ventosas para desplazar las cargas más pesadas.
La correcta organización y la incorporación de los equipos automáticos son fundamentales para garantizar los ciclos requeridos y la óptima realización del picking. Las electrovías recogen los pallets procedentes del depósito directamente de los peines de salida y los sitúan en uno de los cuatro transportadores de entrada a esta zona.
Dos lanzaderas dobles organizan esta área y distribuyen los pallets entre los transportadores de entrada, las estaciones de espera y los puestos de picking. Los pallets origen sobre los que ya se ha actuado en los puestos de picking realizan el mismo recorrido pero a la inversa para regresar al depósito.
Para evitar movimientos innecesarios de los transelevadores y la entrada y salida constante de mercadería en esta planta, se ha habilitado un búfer con 120 posiciones para pallets con elevada rotación que permanecen en espera, también gestionados por dos lanzaderas.
Dos lanzaderas más se encargan de abastecer los puestos de picking con pallets vacíos y de recoger los pedidos una vez finalizados. Acto seguido, los depositan sobre los transportadores que comunican con las electrovías, que los dirigirán al área de consolidación, localizada en un lateral.
Junto a la zona de consolidación, se han instalado unas estanterías de picking manual donde se preparan los accesorios para aquellos pedidos que los precisen.
Una vez finalizados los pedidos, los pallets se trasladan a la enfardadora. Luego, la mercadería permanecerá a la espera de ser enviada a las precargas cuando sea necesario.
Comunicación automática
Las distintas zonas que se hallan en la planta de picking se conectan de forma automática mediante el circuito de electrovías y las lanzaderas.
Las lanzaderas, cuyo cometido es enlazar en línea recta las distintas estaciones y los puestos de preparación de pedidos, están integradas en la zona de picking.
Su gran ventaja es que pueden desplazarse en los dos sentidos y unir estaciones distintas. Se trasladan sobre raíles a una velocidad de 120 m/min e incorporan transportadores de cadenas y de rodillos, así como horquillas telescópicas para mover los pallets.
Las electrovías circulan en un circuito cerrado alrededor de la zona de picking y comunican esta área con la entrada y salida del depósito y la de consolidación.
La elección de la electrovía se debe a que es un sistema de transporte muy ágil y rápido que garantiza un flujo constante de mercadería. Puede desplazarse en curvas y existe la posibilidad de instalar desvíos y atajos.
Se ha diseñado un área de mantenimiento en un lateral del circuito donde se dirigen los carros cuando requieren alguna intervención. Al dejar el suelo libre de obstáculos, las electrovías facilitan las labores de limpieza.
Planta inferior
Área de recepción
La planta inferior del edificio anexo al depósito está distribuida del siguiente modo:
- Transportadores de entrada
- Conjunto de remontadores y dosificadores de pallets vacíos
- Puesto de inspección de pallets y reacondicionamiento
- Circuito doble de recirculado y unión con los transportadores del interior del depósito
- Canales de precargas
- Desremontadora y apiladora de pallets vacíos
- Lanzadera de clasificación
- Muelles de descarga y expedición
La mercadería procedente de producción entra al centro logístico a través de los muelles elevados. La descarga de los camiones se realiza mediante autoelevadores apiladores que permiten introducir los pallets directamente en el circuito de entrada.
En este depósito, la mayoría de los pallets empleados son de una calidad no adecuada y los productos son de un peso muy elevado. Por ello, se ha instalado un conjunto de remontadores que depositan la mercadería sobre pallets esclavos.
A continuación, la mercadería cruza el puesto de inspección para validar que cumple los requisitos establecidos en el proyecto y entra en el depósito.
Salidas del depósito
Los pallets preparados para su envío abandonan el depósito también por el nivel inferior y conectan con el circuito principal de transportadores que los traslada hasta el área de expediciones.
Una lanzadera doble traslada los pallets con la carga y los clasifica en doce canales de precarga. Están formados por transportadores de cadenas y una mesa giratoria en los extremos que facilita que los pallets se puedan recoger por el lado más conveniente en función de su colocación en el vehículo de transporte.
Este sistema posibilita agrupar los pallets de un mismo pedido o ruta y agilizar la operación de carga en los camiones de distribución.
Easy WMS de Mecalux
Se ha instalado el software de gestión de depósito Easy WMS de Mecalux en el centro logístico de Ceramika Paradyż, cuya misión es la de dirigir toda la operativa interna.
Debido a que el depósito es completamente automático, también se ha instalado el módulo de control Galileo que se encarga de garantizar el correcto funcionamiento de todos los dispositivos con movimiento que se utilizan, así como cumplir las medidas de seguridad.
Easy WMS de Mecalux está en comunicación permanente y bidireccional con el ERP de Ceramika Paradyż; ambos se transfieren datos e información fundamental para operar y gestionar el depósito con eficacia y lograr la máxima rentabilidad de los procesos logísticos.
Beneficios para Ceramika Paradyż
- Máximo rendimiento: el depósito automático de Ceramika Paradyż garantiza un flujo constante de productos y un ágil sistema de preparación de pedidos, con una mínima intervención de operarios, lo que elimina riesgos.
- Gran capacidad de almacenaje: el depósito autoportante de 3.290 m2 y 25 m de altura tiene capacidad para más de 20.200 pallets con un peso máximo de 1.500 kg.
- Eficiente gestión del depósito : la operativa del depósito está dirigida y organizada por Easy WMS de Mecalux y el software de control Galileo, cuya función es dar las órdenes de movimiento a todos los dispositivos que componen la instalación.
Depósito automático autoportante de de Ceramika Paradyż Sp. z o.o. | |
---|---|
Capacidad de almacenaje: | 20.256 pallets |
Dimensiones del pallet: | 800 x 1.200 mm y 800 x 1.250 mm |
Peso máx. por pallet: | 1.500 kg |
Longitud del depósito: | 97 m |
Anchura del depósito: | 35 m |
Altura del depósito: | 25 m |
Nº de pasillos de almacenaje: | 8 |
Galería
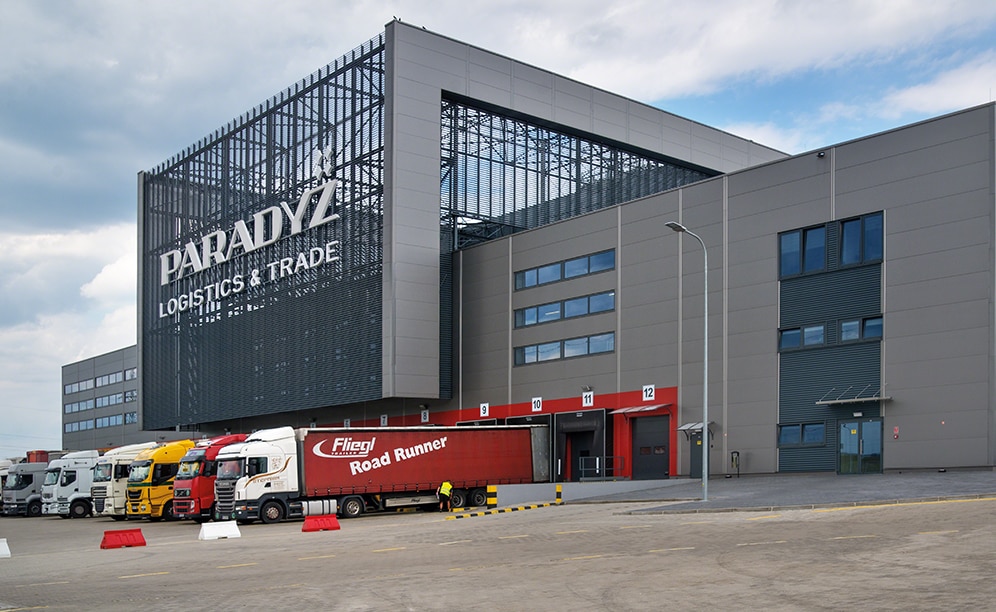
Mecalux ha proyectado para Ceramika Paradyż un almacén automático autoportante con capacidad para más de 20.200 palets
Consulte con un experto