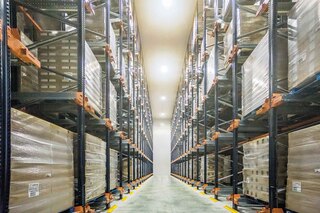
Stock mínimo: ¿qué es y qué estrategias aplicar?
La clasificación del inventario de una empresa en distintos tipos de stock facilita el control y la optimización de los niveles de existencias operativos para su cadena de suministro. Los productos almacenados van disminuyendo en cantidad según se van expidiendo pedidos y, atendiendo a estas fluctuaciones, nos encontramos con dos conceptos clave:
- El stock máximo: viene determinado por la capacidad de almacenamiento que tenga el depósito y por la política de compras o aprovisionamiento.
- El stock mínimo operativo: indica el punto de consumo de existencias en el que es necesario reponerlas, justo antes de llegar a utilizar el stock de seguridad.
La regla del stock mínimo/máximo es uno de los métodos de control de stock más arraigados en las empresas. En nuestro artículo vamos a analizar su alcance, sus limitaciones y cómo lograr optimizar el stock mínimo que hay en el depósito.
¿Qué es el stock mínimo? La regla del stock mínimo/máximo
Con la regla del stock mínimo/máximo, se fija un punto de reaprovisionamiento y, conforme las mercaderías se vayan agotando, se vuelve a hacer un pedido para completar el inventario.
Por ello, su representación gráfica toma la forma de sierra con picos ascendentes que muestran la compra de inventario, y descendentes que evidencian la expedición de estas mercaderías desde el depósito.
Se trata de un método sencillo de implementar y cuya ejecución puede automatizarse con casi cualquier ERP o WMS. De esta forma, cuando un SKU o una referencia llegue al nivel de stock mínimo, el sistema emite una notificación o una orden de reaprovisionamiento automática, liberando así a los gestores de esta tarea.
Existen distintos métodos para fijar los niveles de stock mínimo pero, en resumen, las principales variables que inciden en el cálculo de este parámetro son:
- Las previsiones de la demanda: ¿cuánto se consume de ese SKU en un plazo de tiempo determinado?
- El lead time o tiempo de suministro del proveedor: ¿cuánto tarda en procesar el pedido y que este llegue al depósito?
- El costo (y tamaño) del pedido y las normas del proveedor al respecto.
Representación gráfica de los niveles de stock
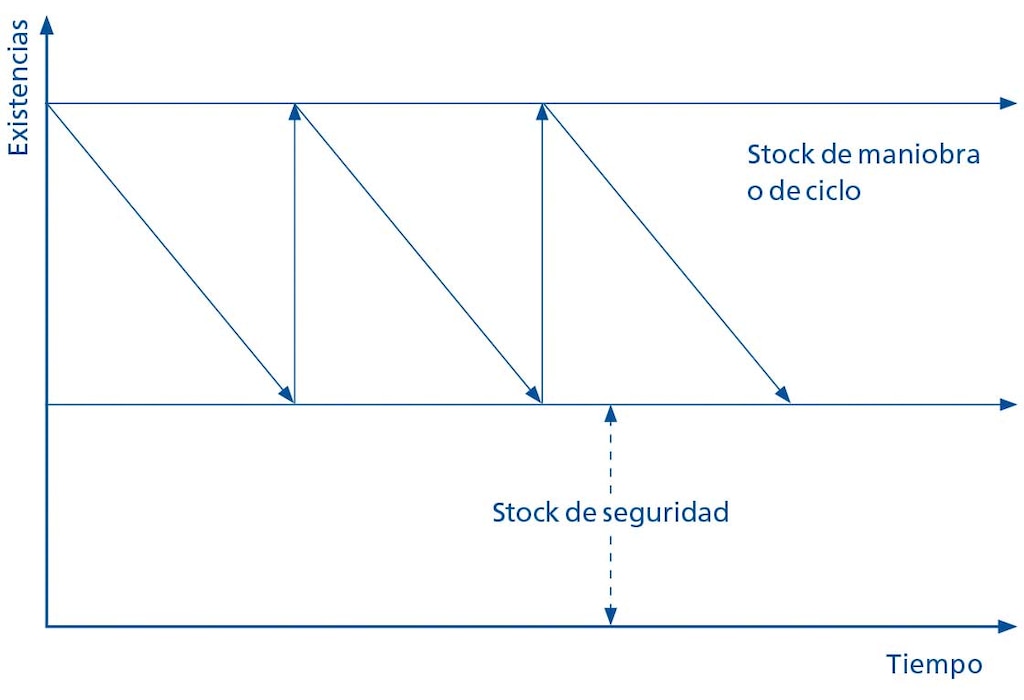
¿Cuáles son las limitaciones de la regla del stock mínimo/máximo?
La regla del stock mínimo/máximo es sencilla y fácil de implementar, de ahí su uso generalizado en muchas empresas. No obstante, esta guía cuenta con limitaciones que conviene mencionar:
- Parte de una perspectiva centrada en cada SKU de manera individual, sin considerar el estado global de los inventarios ni de los proveedores. Por ejemplo, puede haber un proveedor que tenga una política de pedidos que exija a la empresa llegar a un nivel de gasto concreto, pero que puede repartirse entre todos los productos de su catálogo. Con un enfoque de stock mínimo/máximo, el pedido se emitiría cuando se alcanzase ese costo exigido con un sola referencia y no con un conjunto de ellas, lo que puede resultar más beneficioso económicamente.
- No siempre tiene en cuenta la propia evolución de los productos. Cada referencia pasa por un ciclo de vida con varias etapas que influyen en la demanda (introducción, crecimiento, madurez y declive). A no ser que la regla de stock mínimo/máximo esté en continua revisión manual (algo que supondría perder las ventajas de la automatización de ese proceso), aplicar de manera continua el reaprovisionamiento podría suponer acumular costosos sobrestocks.
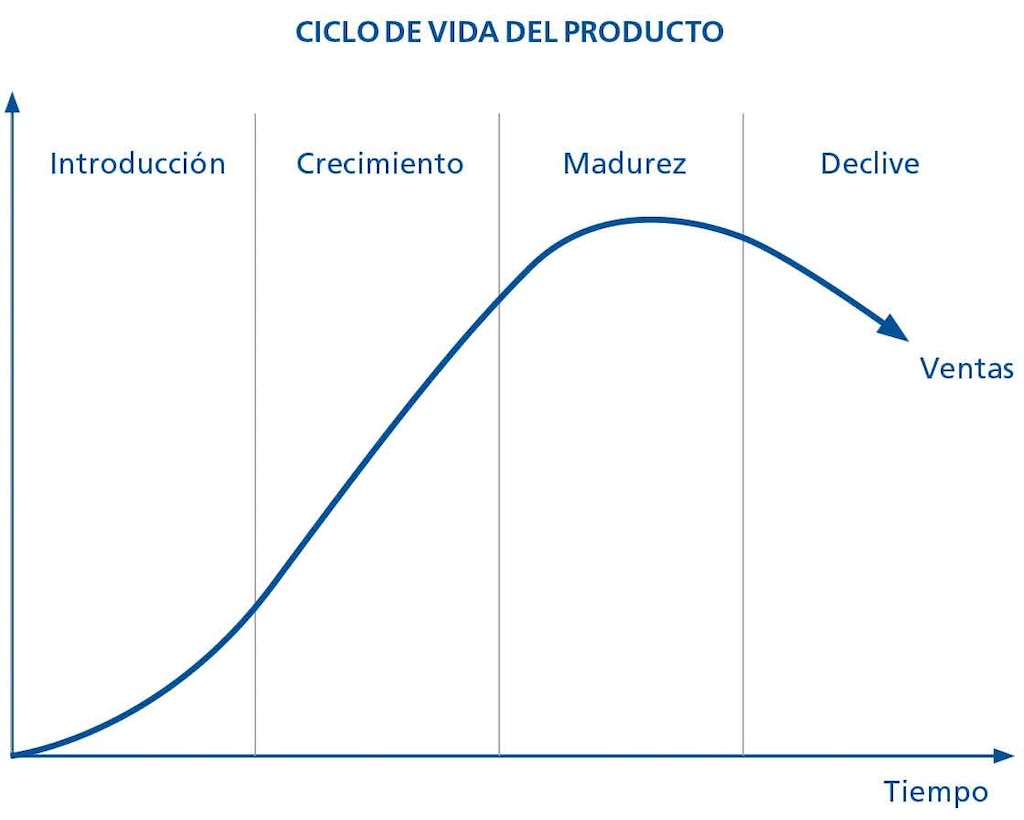
Ventajas de mejorar la gestión del stock mínimo
Una de las consecuencias de aplicar una política de stock mínimo/máximo rígida es terminar acumulando más inventario del necesario. De hecho, la optimización del stock almacenado es uno de los pilares de la metodología Lean logistics, pues las ventajas relacionadas con ello son notorias:
- Disminuye el capital inmovilizado en la tenencia de stocks, inversión que puede ser destinada a otras partidas aliviando la liquidez de la empresa.
- Se rebajan los costos ligados a mantener ese stock, que suponen una partida importante dentro de los costos de almacenamiento logístico. Además, disminuye el riesgo de almacenar inventario de poca rotación que pronto resulte obsoleto y acarree pérdidas para la empresa.
- Se libera espacio en el depósito para nuevos usos: ampliar el catálogo, dotar de más capacidad a la zona de picking o dedicarlo al stock para el que realmente es necesario.
¿Cómo optimizar entonces el inventario para mantener unos stocks mínimos?
Damos algunas recomendaciones a continuación:
- Clasifica el inventario en el depósito y prioriza
Revisando y clasificando el stock almacenado en función de la rotación de existencias vas a sacar a la luz aquel que se haya estancado y esté suponiendo una rémora para la gestión de stock global.
En este sentido, el sistema de gestión de depósitos permite no solo ejecutar conteos cíclicos que comprueben la precisión de los datos de inventario, sino disponer de un valioso histórico que va a facilitar enormemente la tarea de optimización de las existencias.
Además, manejar esta información va a ser de gran ayuda para priorizar los stocks mínimos de aquellas referencias que más interesen atendiendo a distintos parámetros logísticos: rotación, márgenes de rentabilidad, costo de aprovisionamiento…, entre otros. De esta forma, los stocks mínimos de cada referencia deben fijarse desde un punto de vista global y no individual: todos compiten en conjunto por la misma inversión destinada a la adquisición de inventario.
- Planifica más allá de los números que marca el stock mínimo
En ocasiones, la regla de stock mínimo/máximo funciona en un plano paralelo a la realidad, sobre todo si se ha automatizado de tal forma que se cumple estrictamente cuando las existencias tocan el punto de stock mínimo. No obstante, conviene planificar el reaprovisionamiento teniendo en cuenta todos los factores que afectan a las operaciones logísticas y no solo a la cifra del nivel de stock.
De no hacerlo así, el depósito puede verse sobrecargado en la recepción de mercaderías o, si un pedido hecho al proveedor está configurado como envío automático, la empresa pierde ventajas como las que conlleva la consolidación o grupaje de mercaderías.
En cualquier caso, el depósito debe estar preparado para lidiar con imprevistos de este tipo. Contar con un WMS capacita la instalación para ejecutar recepciones ciegas (no planificadas) y organiza la gestión de ubicaciones posterior para esas mercaderías.
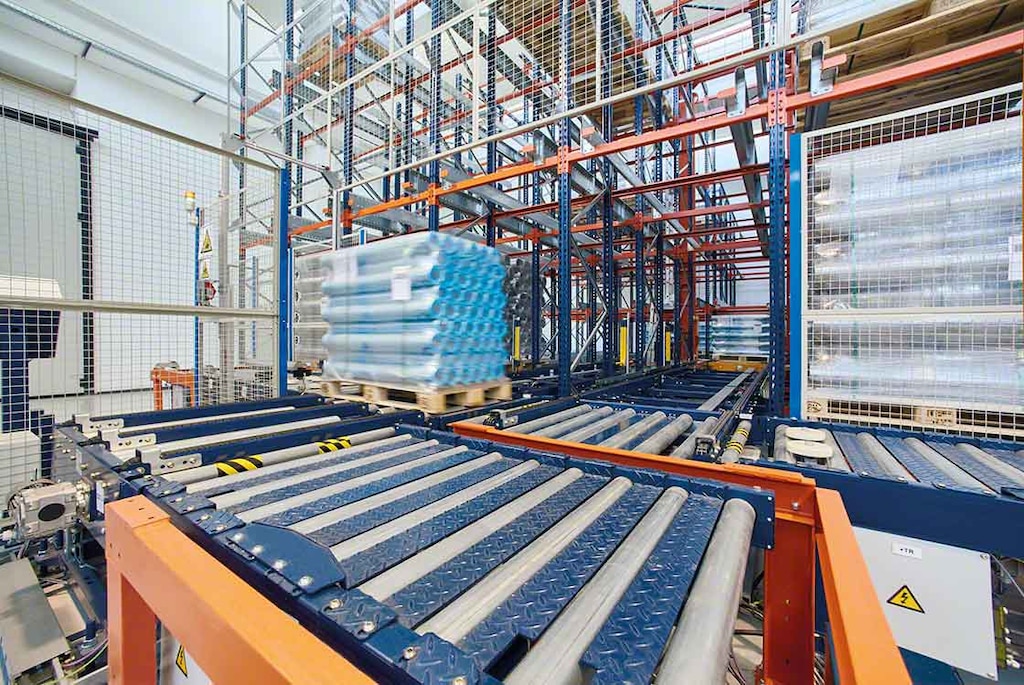
- Apuesta por un depósito más eficiente reduciendo sus costos operativos
La principal función del inventario es dotar a la empresa de capacidad para responder a la demanda en el momento, la forma y el modo adecuado. A pesar de estrategias como el sistema just-in-time, que busca acercarse al paradigma del stock cero, almacenar mercaderías es necesario para el funcionamiento de la cadena de suministro: siempre va a hacer falta.
Partiendo de la base de que hay que tener un stock mínimo, hagamos que el costo operativo sea el menor posible: rebajemos el tiempo que ese inventario necesita estar almacenado. Para ello, un enfoque válido es trabajar por la eficiencia del depósito, mejorando sus tiempos de suministro o lead times. Estos se pueden dividir en dos atendiendo a su naturaleza:
- Lead time físico: hace referencia al tiempo que supone el transporte real de las mercaderías de un sitio a otro. Sin duda, automatizar procesos como los desplazamientos de mercaderías en el depósito libera a los operarios para que estos se entreguen a tareas que aporten más valor.
- Lead time ligado a la información: se refiere al tiempo dedicado a procesar pedidos, tramitar listados de picking y a la organización de cada tarea en correcto orden de prioridad. Los WMS se han formulado como una potente herramienta capaz no solo de reducir los tiempos de ciclo, sino también de perfeccionar la ejecución de las operaciones hasta prácticamente erradicar los errores.
Además, desde el depósito, controlar la dinámica entre los diferentes niveles de stock es fundamental para, por un lado, prevenir las temidas roturas de stock y, por otro, limitar el sobredimensionamiento de las existencias de seguridad.
Aquí también desempeña un papel importante el WMS, ya que aglutina todos los KPI claves para tomar decisiones certeras. En este sentido, destaca el módulo para Easy WMS Supply Chain Analytics Software.
El reto de fijar los stocks mínimos
El impacto financiero de acumular inventarios y la cada vez mayor variabilidad de la demanda han forzado a cambiar el rumbo de la estrategia logística de muchas empresas y a tratar de reducir al máximo los stocks almacenados.
Esto ha revelado las limitaciones de la clásica regla del stock mínimo/máximo. Tratar de ajustarla a una realidad cada vez más compleja pasa por integrar un software especializado en la gestión logística y basar las decisiones en datos medibles.
Si buscas transformar el depósito en una instalación ágil y precisa, no dudes en contar con un WMS a la altura. Contacta con nosotros y te enseñaremos una demo personalizada de Easy WMS con todas sus funcionalidades de control y gestión de stock.